CUTTING FIBER CEMENT BOARD (FCB)
Waterjet cutting is by far the most flexible cutting option when it comes to materials and applications such as smart phone glass manufacturing, motorcycle helmets, fiber cement board cladding (FCB) for homes and commercial buildings, decorative floor inlays, and much more!
ABOUT FCB - WATERJET CUTTING BASICS
Fiber cement panels are used for a wide variety of applications.
They enjoy great popularity as a fire-resistant construction material for building facades. In addition, fiber cement panels are also available for roofing and decorative, intricately cut interior partitions. Accordingly, production plants for fiber cement panels can be found all over the world. The production lines usually run in multi-shift operation, which are expected to run as smoothly as possible and without any unplanned interruptions.
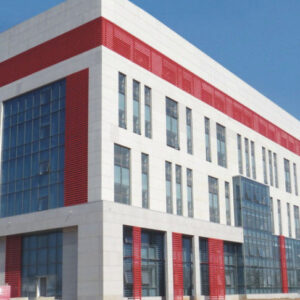
Part of the production line is a cutting station, which cuts the panels to the desired size. Typically these are circular saws that separate the still moist (green) material. Multiple issues associated with blade cutting can be eliminated to a large extent by using KMT’s waterjet cutting technology, which increases production reliability, better finished product quality, and significantly reduces maintenance related downtimes.
CONVENTIONAL BLADE CUTTING CHALLENGES: 
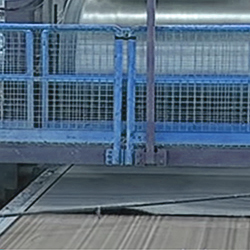
LABOR INTENSIVE | Blade performance must be monitored and replaced often
INCREASED DOWN TIME | Production line must stop for trimming board length
HAZARDOUS WORK ENVIRONMENT | Rotary blade cutting creates excessive dust in the air
LIMITED CUTTING APPLICATION | Blades only cut linear with limited material thicknesses
POOR PRODUCT QUALITY | Rotating blades cause material to “buckle” and leave unfinished, ragged edges
INCREASED DOWN TIME | Production line must stop for trimming board length
HAZARDOUS WORK ENVIRONMENT | Rotary blade cutting creates excessive dust in the air
LIMITED CUTTING APPLICATION | Blades only cut linear with limited material thicknesses
POOR PRODUCT QUALITY | Rotating blades cause material to “buckle” and leave unfinished, ragged edges
WATERJET CUTTING ADVANTAGES: 
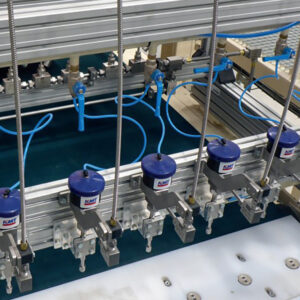
SUBSTANTIAL COST SAVINGS | No tooling, blade sharpening or changing blades–no production line down time
BETTER PRODUCT QUALITY | Uniform surface and cleaner, sharper edge quality–no material distortion
HIGHER EFFICIENCY | Bridge mounted cutting heads slit material instead of moving material under blades
GREATER FLEXIBILITY | Cuts all standard custom thicknesses and can create intricate decorative designs
ENVIRONMENTALLY FRIENDLY | Clean water cutting with no dust expelled into the air
INCREASED PRODUCTION | Waterjet cuts faster with multiple head slitting and cross-cutting capabilities
FAST INTEGRATION | Easy retrofit to existing blade cutting production lines
BETTER PRODUCT QUALITY | Uniform surface and cleaner, sharper edge quality–no material distortion
HIGHER EFFICIENCY | Bridge mounted cutting heads slit material instead of moving material under blades
GREATER FLEXIBILITY | Cuts all standard custom thicknesses and can create intricate decorative designs
ENVIRONMENTALLY FRIENDLY | Clean water cutting with no dust expelled into the air
INCREASED PRODUCTION | Waterjet cuts faster with multiple head slitting and cross-cutting capabilities
FAST INTEGRATION | Easy retrofit to existing blade cutting production lines
RETROFITTING AN EXISTING FCB LINE FOR WATERJET CUTTING: 

- One 50 HP pump running at 45,000psi/3.200 bar
- Five pure water cutting heads including piping and installation materials
- Cutting head orifices can either be 0.17mm/0.007” or 0.15mm/0.006” in size depending on thickness of board
- For a single line, the number of cutting heads running concurrently is 3x